HEAT is the abbreviation of the English "High-Explosive Anti-Tank" of the armor-piercing projectile. At the same time, most of them know that the armor-piercing projectile has another name: the hollow charge armor-piercing projectile or the gather-charged armor-piercing projectile. The chemical energy anti-armored ammunition developed based on the Monroe effect (concentration effect) is mainly used to damage armored targets such as tanks and armored vehicles. It is commonly found in tank guns, anti-tank guns, and anti-tank missiles. The hood is the "heart" of HEAT! However, in fact, the armor-type ammunition cover material is not only copper, nickel, and antimony.
Moreover, the hood is one of the key components of the Sunder Armor Warhead. Its performance will directly affect the quality of the jet (related to whether it can effectively break the armor). Among them, the drug cover material is an important factor affecting the jet velocity and jet length in many parameters of the drug cover. According to experts, the coating material needs to meet the characteristics of high melting point, high density, high sound speed and good plasticity to improve the quality of the jet to a certain extent. At present, the coating materials mainly include pure metals and alloys. Regardless of the alloyed hood, let's take a look at these pure metal hood materials.
1. Copper
Copper is the most commonly used material in pure metal coating materials. This is due to the good density, plasticity and speed of sound of copper, which allows ductile jets to be obtained under explosive loading conditions. In addition, there is another factor that is cheaper. However, armor protection technology is in the dynamic development. Therefore, with the development of armor protection technology, materials such as nickel, tantalum, tungsten and molybdenum with higher density or higher sound velocity have gradually attracted the attention of all countries.
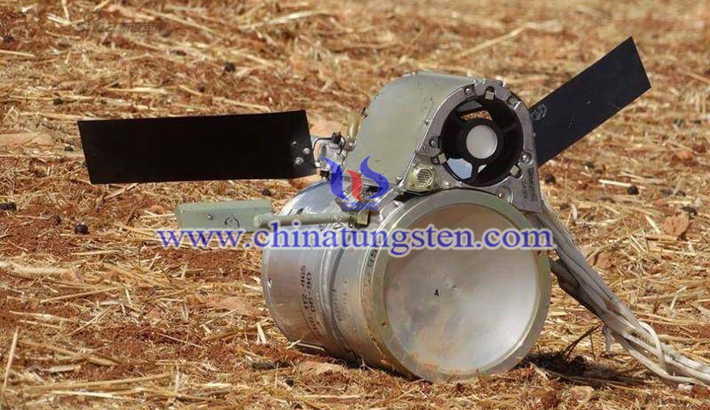
terminal sensitive projectile picture
2. Nickel
The density of nickel is similar to the density of copper. Moreover, like copper, it has excellent plasticity. However, the sound velocity of nickel is higher than that of copper, which allows the jet formed by the nickel coating to have a higher head speed. It has been reported that the nickel hood has a jet flow rate of 15 percent higher than that of the hood. Report data shows that the jet velocity of the jet formed by the nickel liner can reach 11.4 km/sec. In addition, in the early years, the United States has used nickel-type hoods for the Haierfa missile tandem warhead.
3. Tantalum
Tantalum has high density, high sound speed and good dynamic properties. If you are familiar with the German SMArt 155mm end-sensitive bomb, one of the most advanced artillery shots in the world today, you should not miss the use of the enamel material -Tantalum medicine type cover. It is reported that the penetration of the sputum-type hood is increased by 35 percent compared to the copper hood. Not only that, but at the maximum range, the sputum-type hood still ensures the breakdown of the top armor of the tank. Unfortunately, the high cost of cockroaches has seriously hampered the widespread use of this hood.
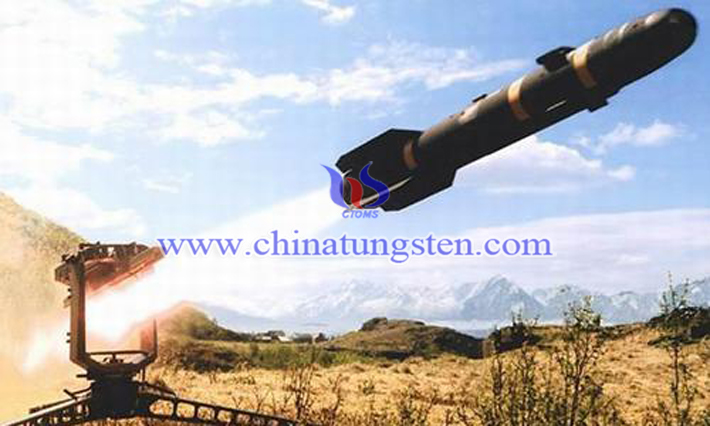
Hellfire picture
4. Tungsten
According to the literature, tungsten is an extremely ideal coating material. From the following points: First, tungsten has the advantages of high density, high sound velocity, high melting point, etc. Moreover, tungsten has high dynamic plasticity and can form long and the continuous jet, which is due to the fact that tungsten is a body-centered cubic metal, and there are many slip systems. It is reported that the British Ministry of Defense has successfully produced a pure metal tungsten coating, and its armor performance is significantly higher than the pure copper coating. According to the data, the jet length of the pure copper coating is only about 670 mm, while the jet length of the pure tungsten coating extends to about 880 mm. The US Army, as early as 1998, has determined the goal of replacing the copper hood with a tungsten-type hood in 2005-2013.
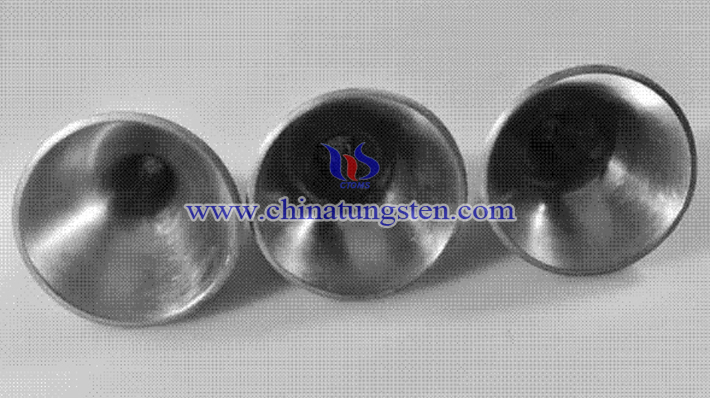
tungsten alloy liner picture
5. Molybdenum
Molybdenum may also be a material that is less familiar to everyone. According to the literature, molybdenum has a high sound velocity and high density, and is also a relatively good coating material. Earlier, the US Army has conducted extensive experimental research on the molybdenum hood and its jet characteristics. They found that the molybdenum hood has good jet flow and its jet head speed can reach up to 12.5 km/s.
However, in fact, no matter which kind of pure metal is used, there are still many problems with these pure metal coatings. For example, the increase in jet length needs to be achieved by increasing the jet velocity gradient, however it is difficult to increase the jet velocity gradient with a pure metal liner. Also, although tungsten and molybdenum and niobium can increase the density of the liner, their process difficulty and manufacturing cost are greatly increased. Therefore, the alloy hood has appeared!